Release Notes for Coreform Flex 2025.3
Find our verification manual here.
Find our reference manual here.
For easy access to both, go to docs.coreform.com
Released: 31 March 2025
Table of Contents
New features
More robust trimming
Tet meshing is the incumbent fully automatic meshing solution for complex geometries, but its success is still dependent on the ability to build a valid surface mesh on the CAD. Coreform has developed trimming that is robust over many CAD issues. Internal testing on a repository of 2000+ customer-provided parts, benchmarked against the tet meshing capabilities in Coreform Cubit, found Coreform Flex trimming to be more robust than the tet mesher.
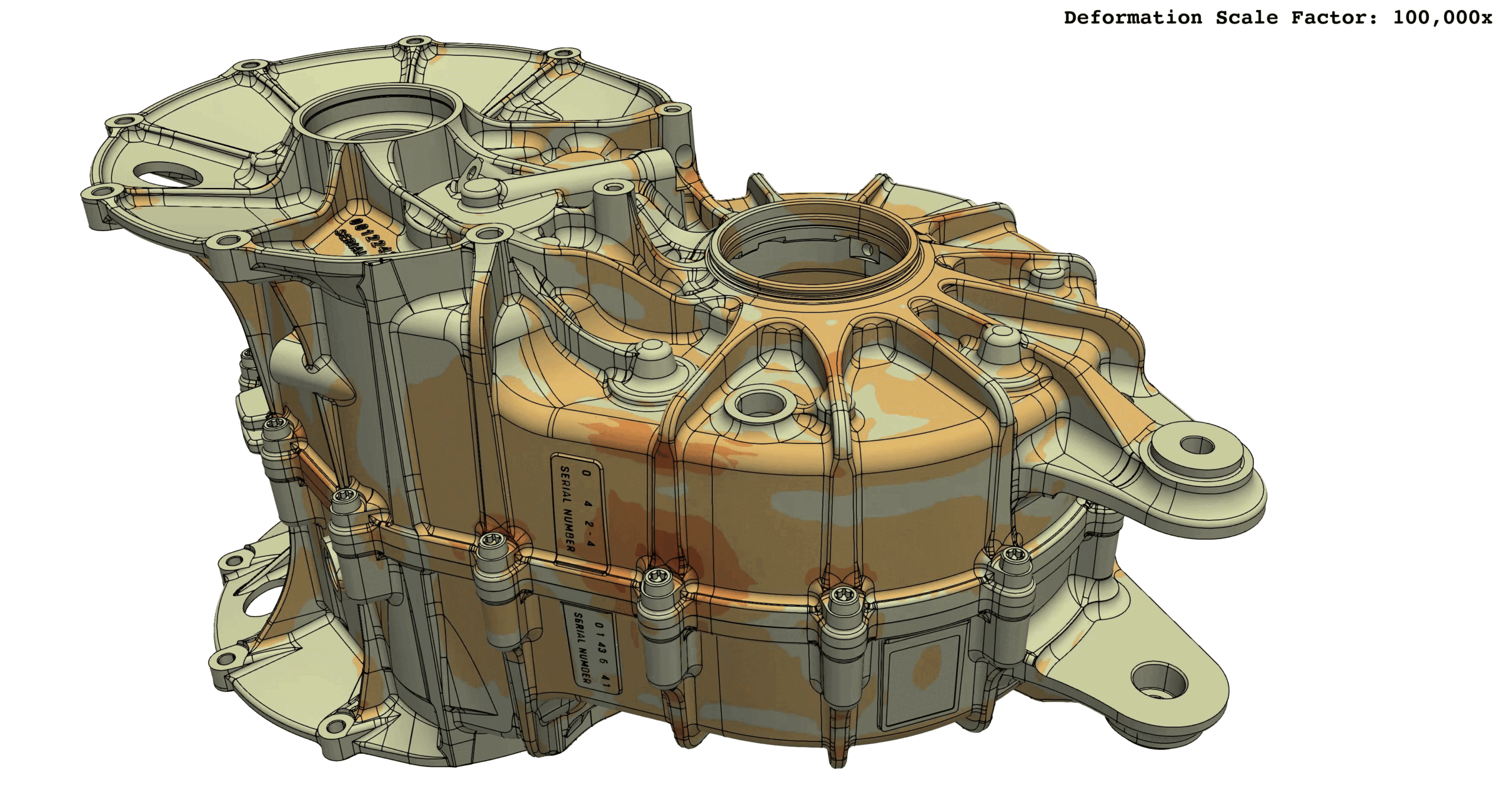
A fully featured CAD model trimmed and used in a nonlinear simulation in Coreform Flex
A trimmed model in the Flex GUI
Neo-Hookean elasticity
This release implements a two-parameter, isotropic hyper-elastic neo-Hookean material that converges to the linear elastic model in the small deformation limit. This should be used in place of linear elasticity for large deformations, even if they are strange or small. This also includes an extension of this model for nearly incompressible solids which is available via a pressure stabilization approach. More information can be found in our reference manual.
Our public verification manual includes the following verification tests:
- https://docs.coreform.com/content/iga-verification/iga-verification-benchmarks-solid-mechanics.html#%28part._large-and-small-deformation-of-composite-geometry-with-material-interface-connections-and-merged-surfaces%29
- https://docs.coreform.com/content/iga-verification/iga-verification-benchmarks-solid-mechanics.html#%28part._neo-hookean-cylindrical-pressure-vessel%29
Our public reference manual includes the following:
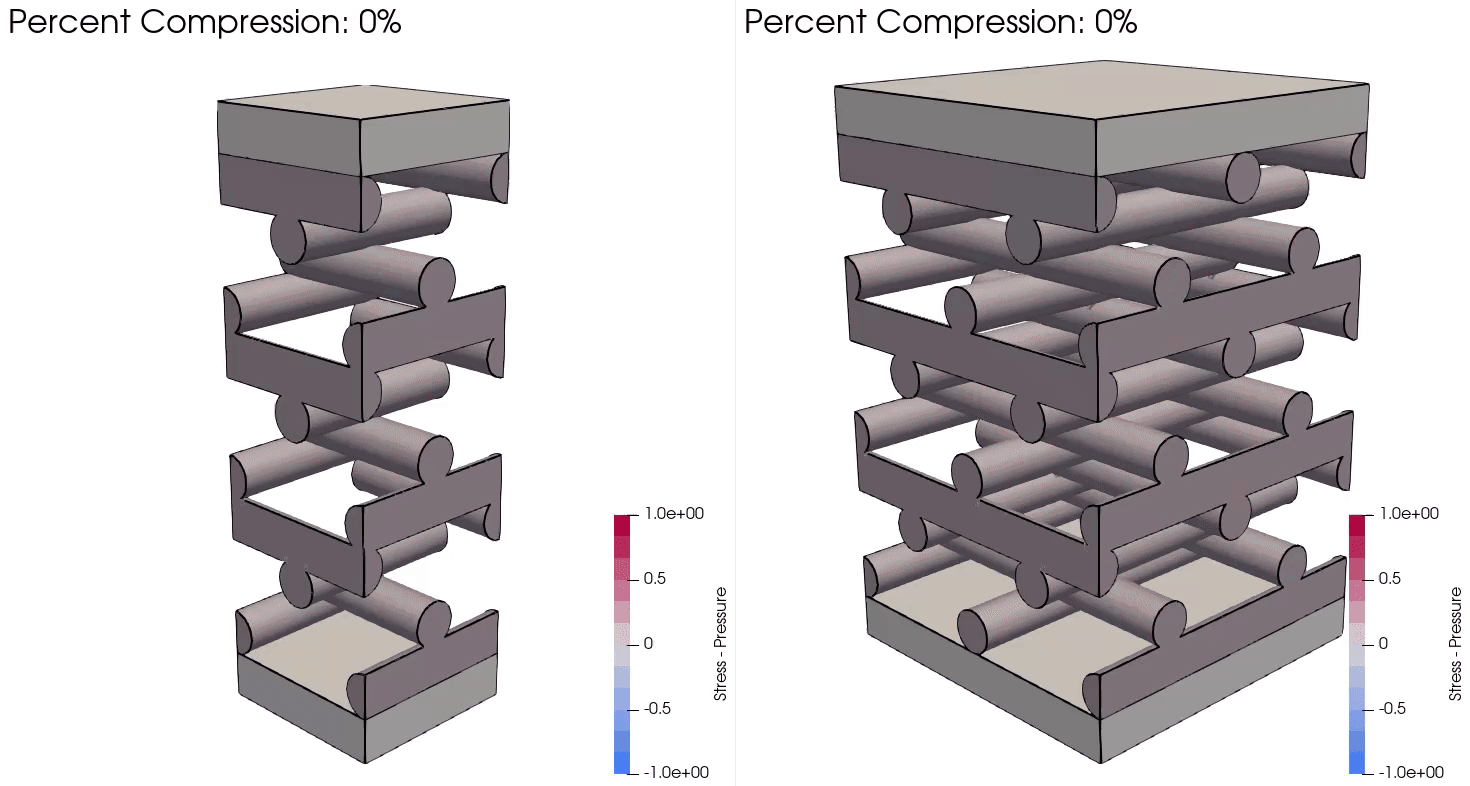
Compression of a direct-ink write silicone pad. Model setup is drastically-simplified due to the automatic selection of contact parameters.
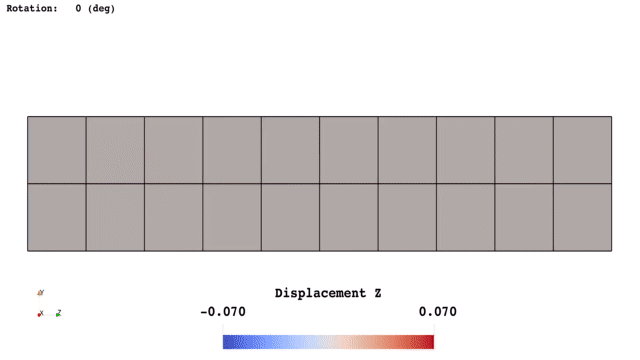
An animation of one of our verification tests demonstrating the robustness of the neo-Hookean elasticity model for large deformations.
Mooney-Rivlin elasticity
We have implemented the three-parameter isotropic hyperelastic Mooney-Rivlin material model. This also includes an extension of this model for nearly incompressible solids is available via a pressure stabilization approach.
Our public verification manual includes the following verification tests:
Our public reference manual includes the following:
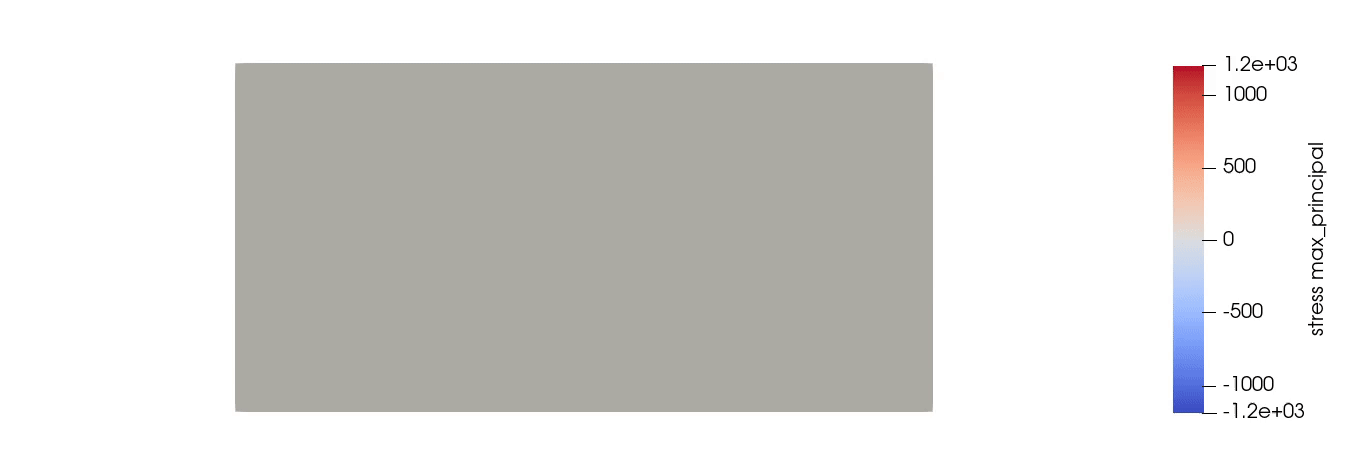
An animation of one of our verification tests for the pressure-stabilized Mooney-Rivlin material model for a nearly-incompressible material. Deformation of this nearly incompressible material (Poisson’s ratio = 0.49999) is modeled using a Mooney-Rivlin material model with a stabilized formulation to alleviate locking.
Neo-Hookean isotropic plasticity
This material model combines the neo-Hookean elasticity material model with a nonlinear isotropic rate-independent plasticity model based on J2 flow theory.
Our public verification manual includes the following verification tests:
Our public reference manual includes the following:
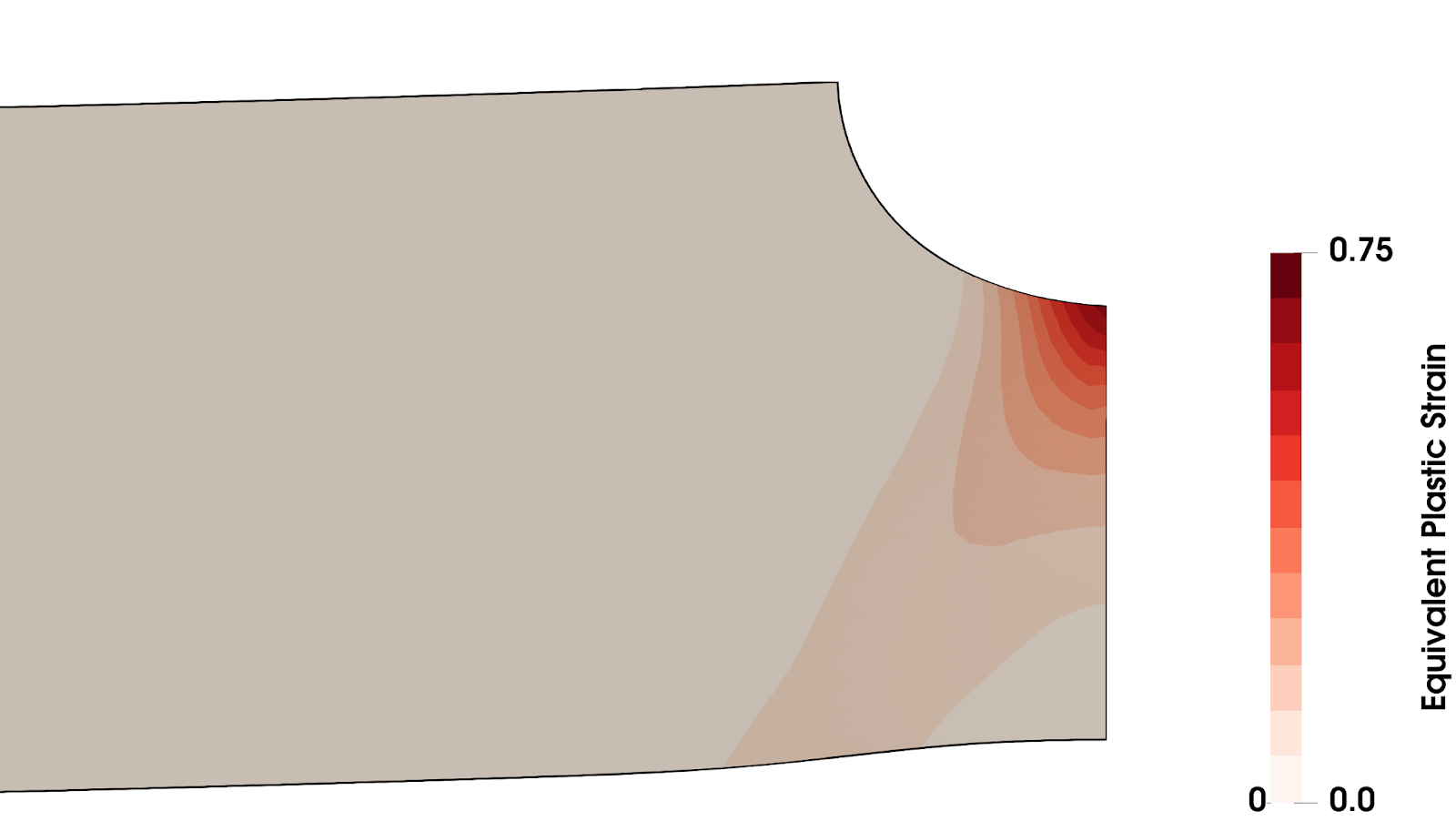
A snapshot of one of our verification tests for the neo-Hookean isotropic plasticity model.
Improved boundary condition workflow
Coreform Flex weakly enforces Dirischlet boundary conditions such as displacements. This eliminates the interdependence of boundary conditions, CAD, and mesh, but does require some parameters to be selected. In this release we have implemented automatic physics-based parameter selection that further simplifies the workflow.
Our public reference manual includes the following:
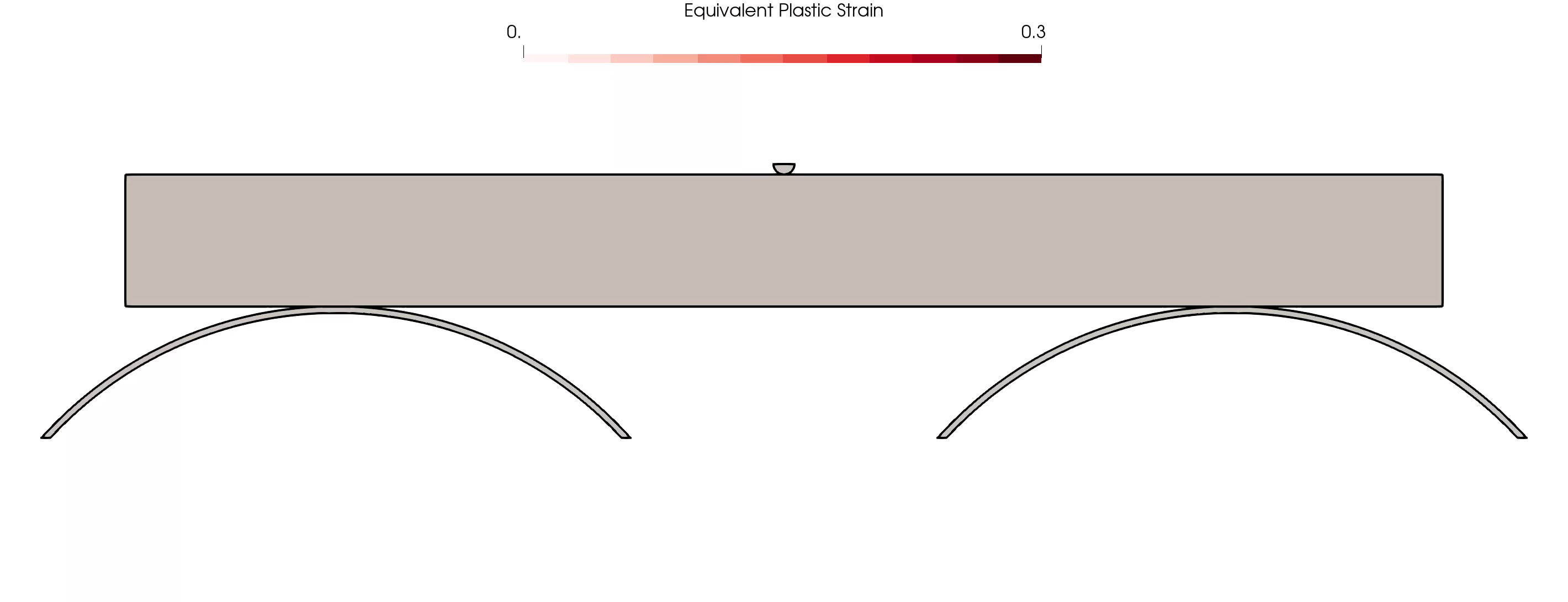
One of our verification problems that demonstrates the automatic estimation of weak-enforcement parameters for boundary conditions. This problem also includes mechanical contact, with automatic parameter estimation, as well as the neo-Hookean isotropic plasticity model and the implicit dynamic solver – further demonstrating all the other features of this release working in unison with the automatic weak-enforcement parameters’ estimation.
Nonlinear continuation solver
Coreform 2025.3 implements an implicit static timestepping method based on a numerical continuation. This improves the ability to converge on difficult nonlinear problems. To achieve this, a scaling parameter is created that describes the distance from the initial state to the final state. Note that parameter is referred to as “time” even though this method ignores mass contributions. This also supports a simple initial adaptivity scheme, e.g., reducing the timestep if a nonlinear substep fails, or increasing the timestep upon success.
Our public verification manual includes the following:
- https://docs.coreform.com/content/iga-verification/iga-verification-benchmarks-solid-mechanics.html#%28part._mooney-rivlin-material-verification%29
- https://docs.coreform.com/content/iga-verification/iga-verification-benchmarks-solid-mechanics.html#%28part._large-and-small-deformation-of-composite-geometry-with-material-interface-connections-and-merged-surfaces%29
- https://docs.coreform.com/content/iga-verification/iga-verification-benchmarks-solid-mechanics.html#%28part._neo-hookean-cylindrical-pressure-vessel%29
- http://idocs.coreform/html/iga-verification/iga-verification-benchmarks-solid-mechanics.html#%28part._iga-verification-benchmarks-solid-mechanics-mechanical-contact%29
Our public reference manual includes the following:
Mechanical contact
We now have material contact in Flex. With this 2025.3 release, Coreform Flex has an initial implementation of mechanical contact that works for both body-fitted and immersed flex approaches. This release includes initial capability; increased robustness and performance are being worked on.
Our public verification manual includes:
Our public reference manual includes:
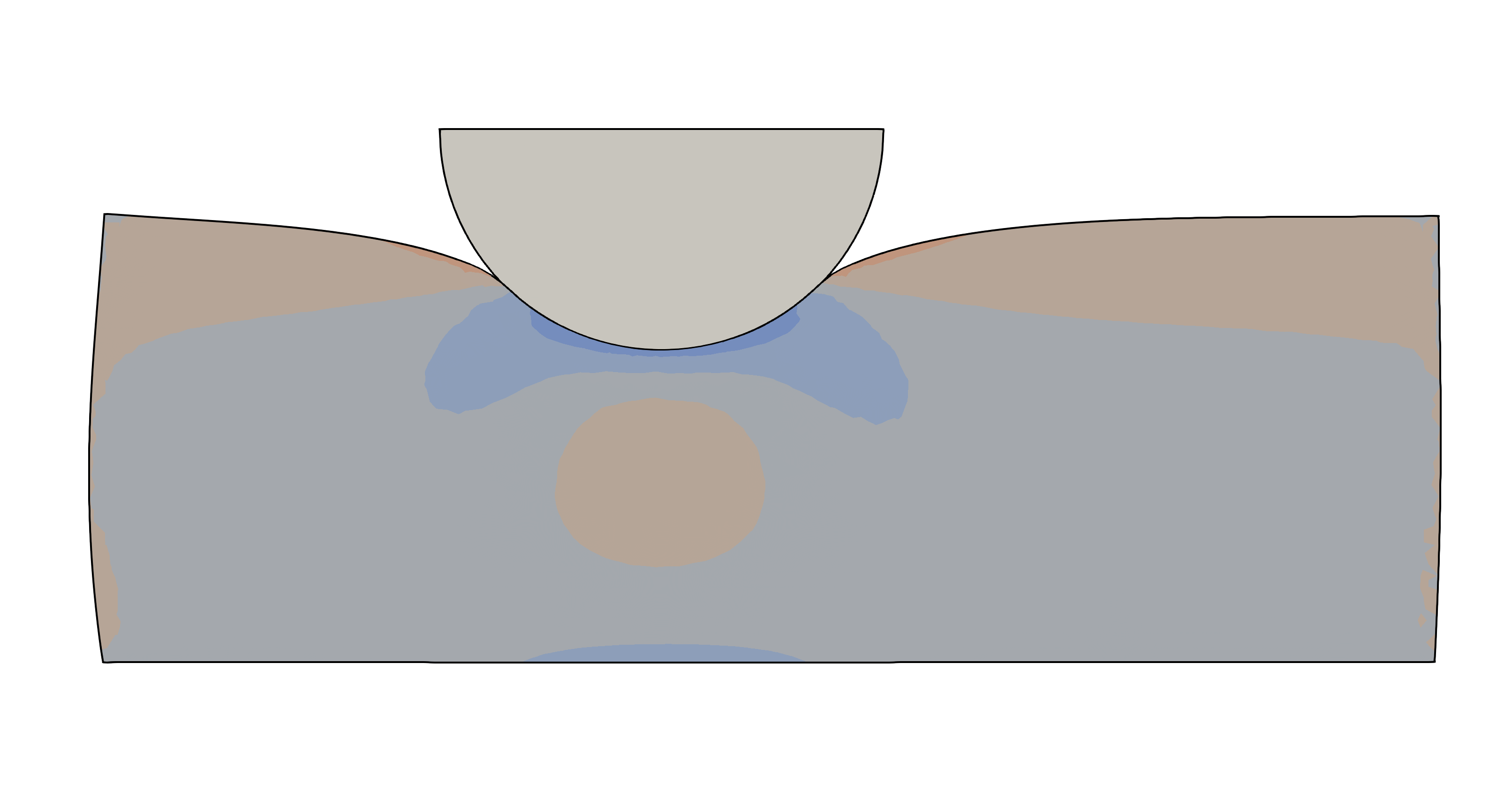
Snapshot of results from one of our contact verification tests. The cylinder is moving to the right, nearly-symmetric contours of the tangential stress component demonstrates the frictionless contact model.
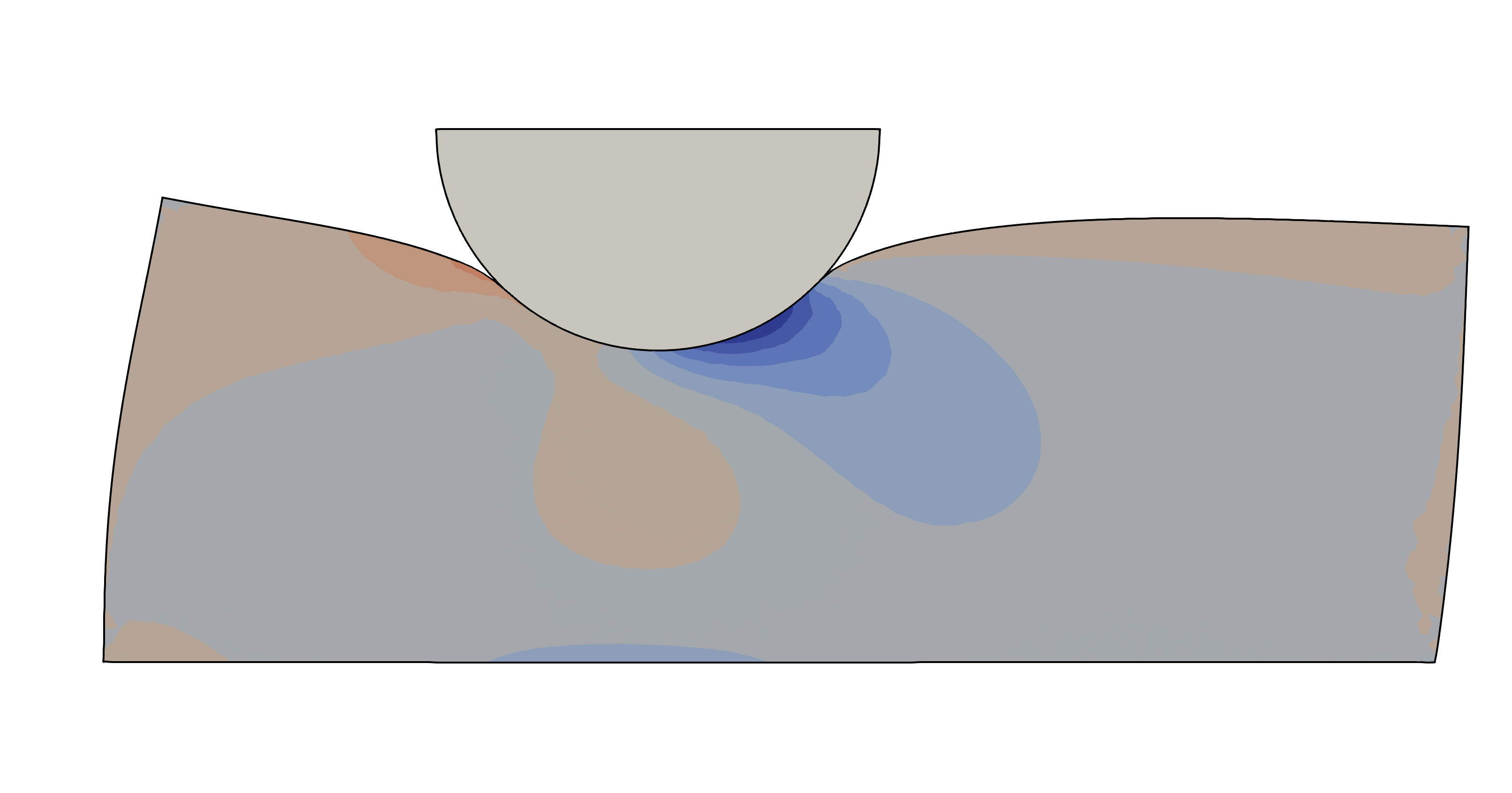
Snapshot of results from one of our contact verification tests. The cylinder is moving to the right, the unsymmetric contours of the tangential stress component demonstrates the Coulomb friction contact model.