Solutions / CAPABILITIES
Unleash the power of next-gen FEA with Coreform
Whether you want to radically improve your simulation process by running accurate FEA simulations directly on fully-featured CAD, or just get better results with your existing solver, Coreform can help.
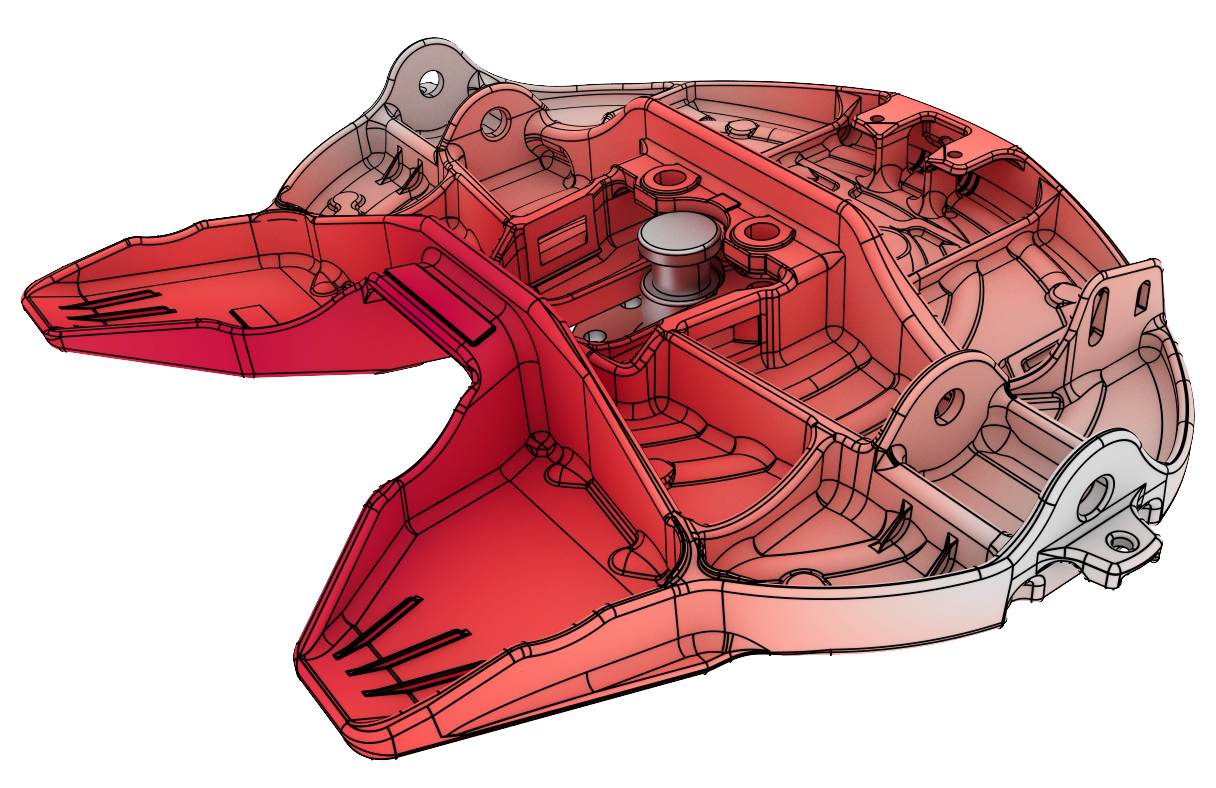
Simulation Without Compromise
Coreform is a pioneer in advanced solutions for engineering simulation. Our groundbreaking approach to finite element analysis harnesses the power of Isogeometric Analysis (IGA) to seamlessly integrate CAD and analysis. Coreform eliminates the need for traditional meshing and geometry simplifications, preserving the fidelity of original designs throughout the simulation process.
However, we realize that engineers are often conservative, and there are many workflows built on decades-old techniques that do require meshes. Our team cut our teeth developing some of the industry’s best meshing software, and we sell this as well! So whether you are looking to become an early adopter of the next-generation of simulation, or just looking to optimize your current process, we would love to talk with you. Coreform empowers engineers to tackle the most challenging simulations faster and more efficiently, transforming workflows across industries such as nuclear, aerospace, automotive, civil engineering, and biomechanics.
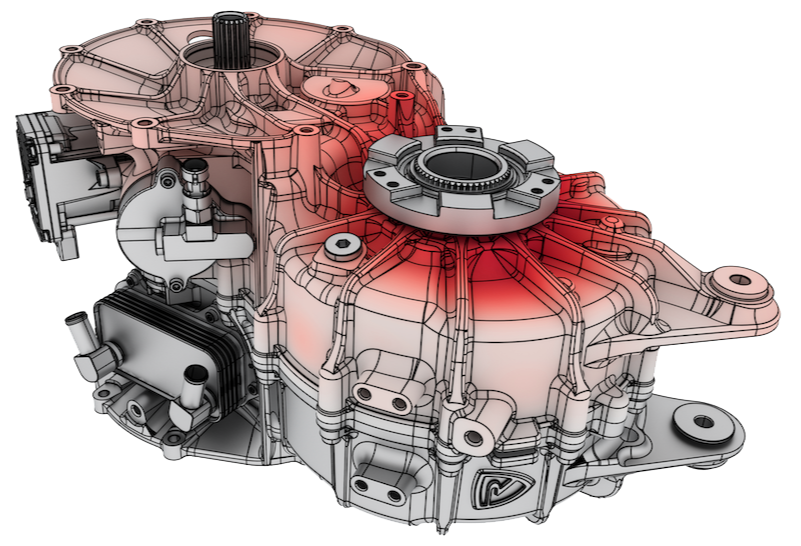
Key Capabilities
Isogeometric Analysis
Direct CAD Simulation
Computational Fluid Dynamics
Fluid and Gas Simulation
Key Capabilities
Finite Element Analysis
Performance Prediction
Neutronics
Neutron Behavior Simulation
Isogeometric Analysis (IGA)
IGA is a finite element method that directly integrates CAD models into the analysis phase, eliminating the need to create a conformal mesh from the CAD, which is often a source of error and inefficiency in traditional finite element analysis (FEA). Coreform’s IGA approach also eliminates the time-intensive stages of model defeaturing or midsurfacing that are common in traditional FEA, leading to more accurate and efficient simulations.
Benefits:
- Exact Geometry: Maintains true CAD geometry, avoiding approximations that can skew results.
- Greater Accuracy: Produces more accurate simulations for complex shapes, thin-walled structures, and freeform geometries, leveraging the superior accuracy of CAD math directly in the solution.
- Faster Time to Solution: Reduces the time spent on meshing and geometry correction, speeding up the entire simulation process.
- Automatable: The Coreform Flex preprocessor is fully automatable via Python, enabling rich design exploration.
Finite Element Analysis (FEA)
FEA is a simulation method used in engineering to predict how structures and components will respond to external forces, such as stress, heat, and vibration. Coreform can improve your FEA workflow both through our next-generation IGA approach as well as through superior meshing technology for traditional FEA workflows.
Coreform’s IGA technology is based on the same Galerkin methods as FEA, enhanced to leverage highly accurate CAD math instead of the low-order math traditionally used to compute solutions. This yields higher accuracy and smoother representations of complex geometries, particularly for industries requiring precise structural analysis, such as defense, nuclear, and aerospace.
In addition, Coreform offers superior meshing technology that can fit seamlessly in a traditional FEA workflow. Coreform’s meshing software offers superior quality hex meshing, as well as oustanding tet meshing capabilities, and can be fully scripted via Python.
Benefits:
- Higher Accuracy for Complex Structures: Traditional FEA faceting meshing can be replaced and enhanced by Coreform’s IGA approach, which eliminates geometry errors with CAD-exact models that smoothly match real-world shapes, even with coarse element densities.
- Reduced Meshing Errors: Coreform’s approach allows for zero geometry errors that arise from faceted mesh generation, providing a more reliable analysis from start to finish.
- Flexible Boundary Conditions: Enables the easy application of complex boundary conditions and constraints for advanced simulations.
- No limitations: Coreform eliminates limitations relating to phenomena like thin shell buckling/large deformations, shear locking, sliding contact, crack and fracture propagation discontinuities, and spurious spectral and boundary layer oscillations.
- Automation: All Coreform solutions can be automated by Python scripting.
- Integration with current workflow: Coreform’s best-in-class traditional meshing integrates with leading commercial and open-source FEA solvers.
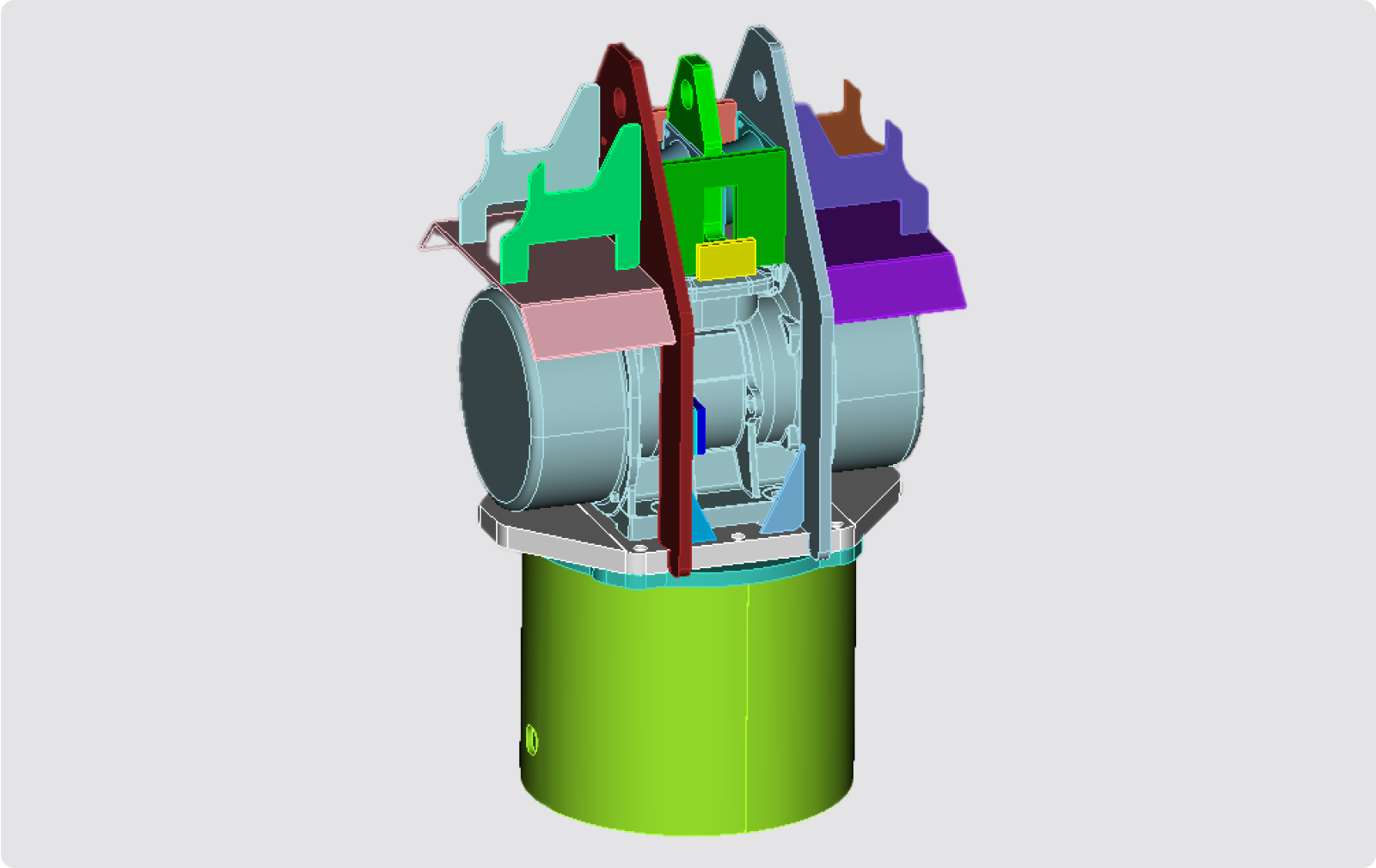
Computational Fluid Dynamics (CFD)
CFD is used to simulate the behavior of fluids—gases and liquids—around and within objects. With Coreform’s unique approach, engineers can prepare high-quality meshes for fluid dynamics on geometries that are challenging for traditional CFD tools, ensuring more accurate results. This allows an optimized process for analyzing complex fluid flow problems, providing more precise simulations in industries such as aerospace, automotive, marine engineering, and automation industries.
Benefits:
- Hex Meshing: Coreform Cubit offers advanced hex meshing, which improves the quality and accuracy of computational fluid dynamics (CFD) simulations by generating structured, high-quality grids that produce more accurate simulations with lower computational costs.
- Python API and Process Automation: Coreform software has a powerful scripting language and Python API. The automation features allow users to reuse mesh generation processes, significantly reducing repetitive manual tasks and customizing meshing workflows, offering enhanced flexibility for adapting to complex projects.
- Comprehensive toolset for streamlining CAD prep: The Coreform Cubit GUI is intuitive and user-friendly, making it easy for new engineers to learn. The command panel and model-building tools enable users to create and mesh models in just a few minutes.
- Reduction in Meshing Time: Coreform Cubit accelerates the overall simulation process by cutting down the time spent on meshing.
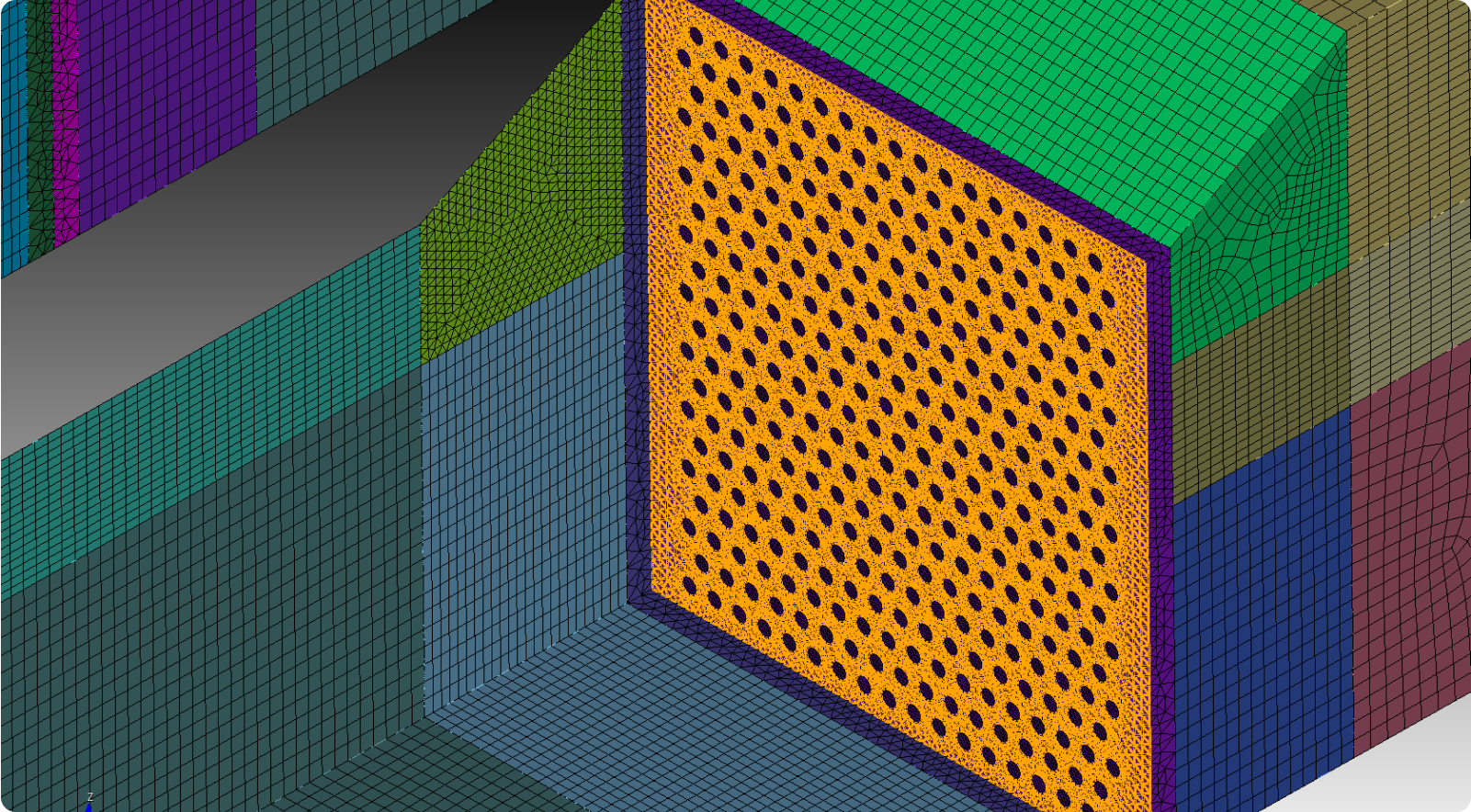
Mesh at an inlet stilling baffle plate generated using Coreform Cubit. Automatic tet meshing for the baffle plate was used to quickly and accurately capture the geometry, while using semi-automatic hex meshing to represent the surrounding channels for efficiency. The baffle plate consists of many small (~1-inch holes) that need to be accurately captured within a larger channel to adequately calculate the system hydraulics.
Courtesy of Carollo
Neutronics
Neutronics refers to the simulation of neutron behavior in nuclear systems, such as reactors and other energy applications. Coreform’s neutronics capabilities allow for accurate modeling of neutron transport, absorption, and reaction rates, making it an essential tool in the nuclear energy industry, research, and safety analysis. By integrating neutronics with Coreform’s advanced meshing and analysis tools, engineers can obtain highly detailed and reliable simulations of nuclear systems.
Benefits:
- Accurate Neutron Transport Modeling: Coreform uses DAGMC (Direct Accelerated Geometry Monte Carlo) to provide precise modeling of neutron transport in complex reactor geometries, ensuring better prediction of behavior in nuclear systems.
- CAD-based Multi-Physics Integration: Geometry prepared in Coreform Cubit for neutronics can be coupled with other physics, such as thermal and structural analysis, for full reactor simulations, allowing engineers to analyze the impact of neutron flux on reactor materials and cooling systems.
- Efficiency in Simulation Setup: Coreform’s ability to work with complex geometries without requiring mesh simplification is critical for accurate neutron behavior analysis, as simplifications can lead to incorrect predictions in reactor design.
- OpenMC integration: Coreform Cubit is an outstanding tool to prepare OpenMC simulations, with workflows supporting OpenMC Constructive Solid Geometry (CSG) import into Coreform Cubit for 3D visualization and hybrid model creation, and DAGMC output to OpenMC, and visual debugging tools for lost particle tracking.
- Comprehensive Reaction Rate Predictions: Simulates neutron-induced reactions, enabling engineers to predict fuel depletion, radiation damage, and energy generation with greater accuracy.
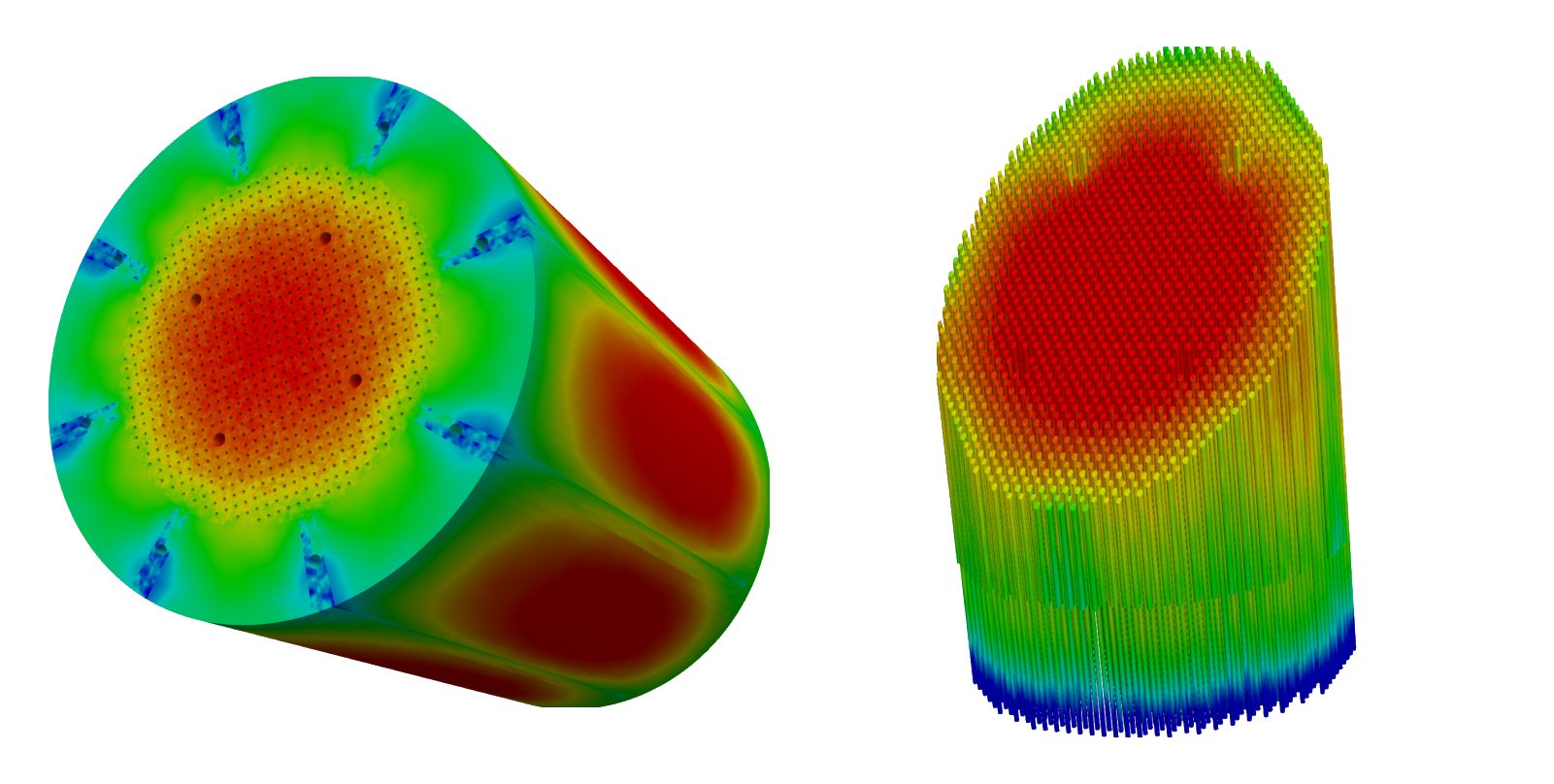
Plots for neutron and prompt fission gamma fluxes for a gas-cooled, graphite-moderated nuclear reactor. The system has been modeled with mesh generated in Coreform Cubit and simulated using MCNP6.3. These plots demonstrate the superiority of unstructured mesh modeling over constructive solid geometry (SCG). Courtesy Ibrahim Attieh.
Advantages
Unmatched Precision and Accuracy
Coreform’s innovative Isogeometric Analysis (IGA) technology enables engineers to use exact CAD geometry in simulations, eliminating the need for geometry simplifications and mesh approximations that can compromise accuracy. Even the most complex geometries are represented with precision, leading to highly accurate simulation results. This precision is especially valuable in fields where even minor deviations in geometry can lead to significant performance differences, such as aerospace, automotive, or nuclear energy.
Faster Time to Solution
Coreform dramatically reduces the time required to move from design to analysis. By using CAD models directly, engineers can bypass time-consuming mesh generation and cleanup processes that are necessary in traditional FEA workflows. Coreform’s automated meshing and advanced solver enable faster setup and execution of simulations, which translates to shorter project turnaround times. Engineers can focus more on problem-solving and innovation rather than wrestling with model preparation, making Coreform a valuable tool for accelerating development cycles.
Reduced Cost of Product Development
Coreform reduces product development costs by streamlining the engineering workflow and minimizing time spent on model preparation. With fewer steps required for geometry preparation, meshing, and model validation, engineers can iterate faster through design and analysis cycles. The ability to perform linear and nonlinear analyses enables simultaneous testing and optimization of various design aspects. This enhanced efficiency reduces bottlenecks, accelerates project timelines, and allows teams to deliver higher-quality results, ultimately lowering overall development costs.

“Our production team has used Coreform Cubit extensively on a daily basis across the team for over five years. We have found Coreform Cubit to be a fully comprehensive, powerful, fast and intuitive meshing tool, which our customers often end up using as well. We have built many plugins to our software that run Coreform Cubit meshes automatically based on Python scripts. Coreform Cubit remains our preferred meshing technology.”
Phuong Huynh
Founder and Head of Research & Operation
Akselos
See why Coreform Cubit is trusted by government and industry leaders around the world
From nuclear energy to automotive, Coreform Cubit’s performance and capabilities consistently deliver.
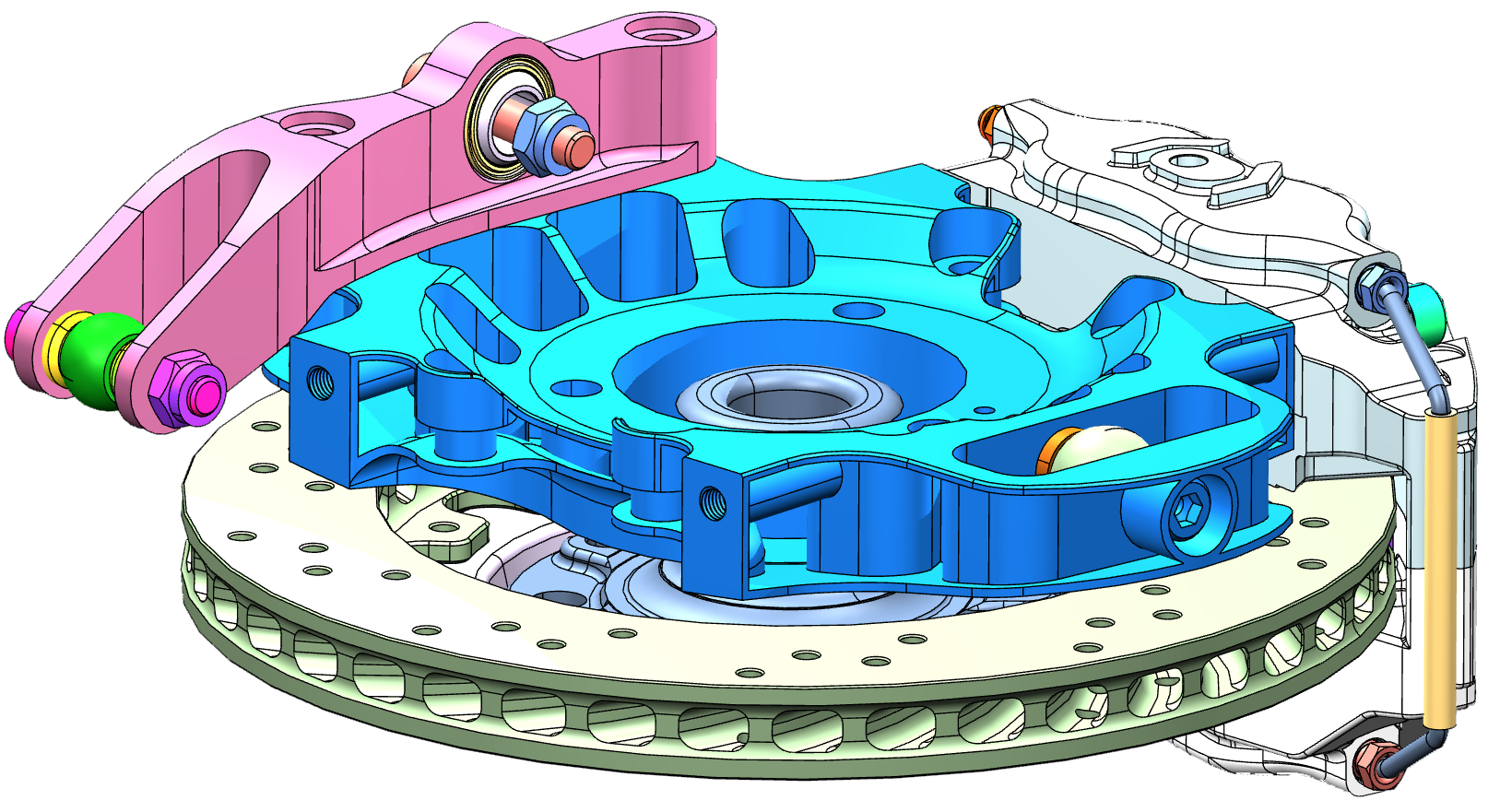
Courtesy Sandia National Labs