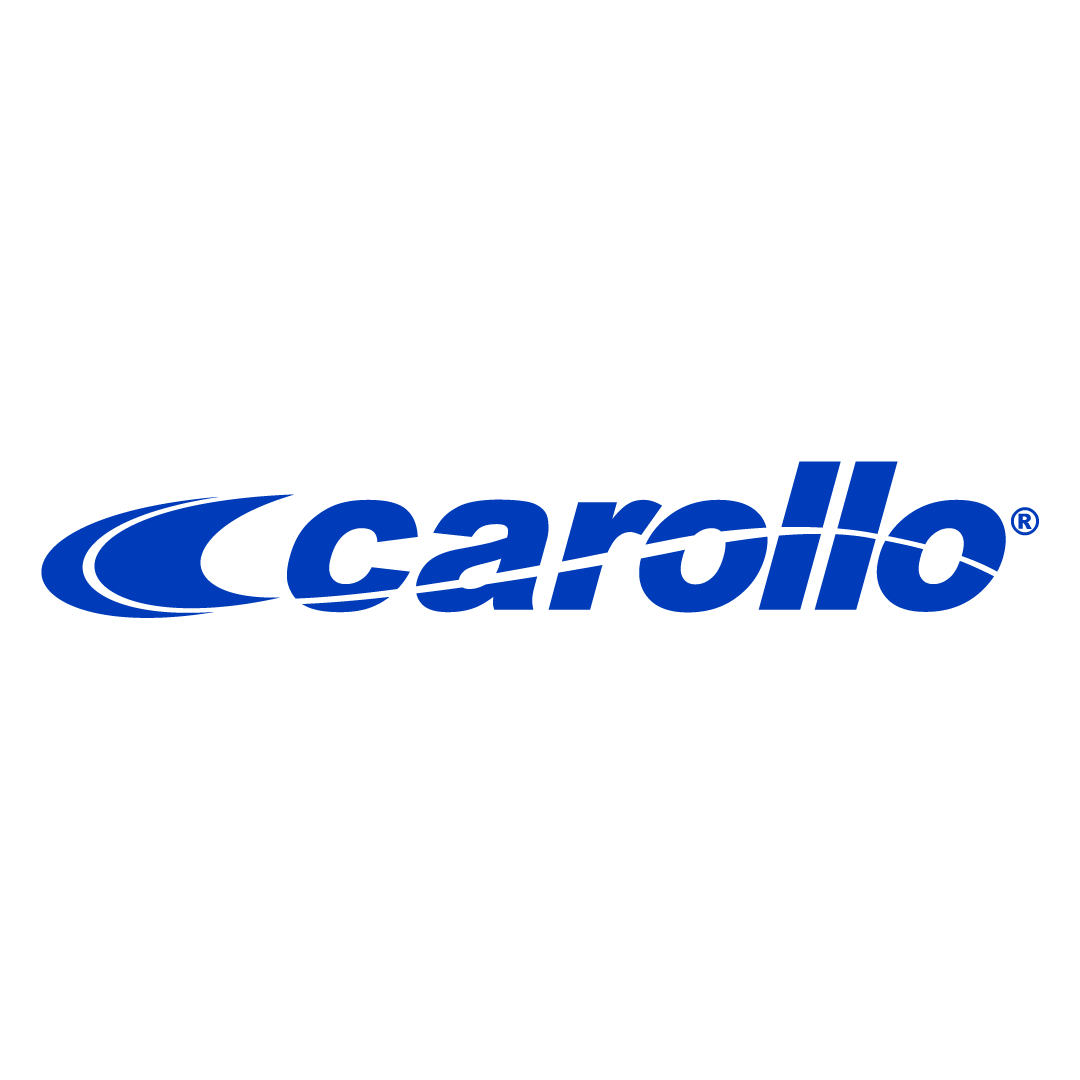
Our team has been using Coreform Cubit for CFD meshing since 2015 when we switched over from GAMBIT. Cubit is a reliable meshing software capable of building very large and complex computational meshes for CFD simulation that just works!
Ed Wicklein
Principal Technologist,
Background
Carollo Engineers is the largest firm in the United States whose focus and practice, since 1933, have been dedicated solely to water-related engineering. The Carollo Research Group is a diverse team of engineers, scientists, and researchers located in offices across the country who work collaboratively to connect fundamental and applied research to practical, innovative, and reliable water solutions for their clients.
Carollo is an industry-leading pioneer in the use of computational fluid dynamics (CFD) as a critical hydraulic and process design tool, with over 30 years of experience applying this technology to their daily work. Their portfolio of applications ranges from projects that improve pump station hydraulics, optimize disinfection processes, and model sedimentation to operational simulations of complete treatment plants.
Problem
To run accurate CFD simulations, Carollo first creates high-quality mesh representations of their geometry, which they then send to various CFD solvers, including ANSYS Fluent. When Carollo first began their CFD work decades ago, they chose the venerable GAMBIT meshing software to create these representations. In 2015, Carollo reevaluated their CFD meshing needs and decided to upgrade their software to Coreform Cubit.
Solution
Carollo’s optimal CFD meshing choice is Coreform Cubit for the following reasons:
-
Up-leveling with familiarity: Though it boasts additional advanced meshing capabilities, Coreform Cubit has a similar workflow to GAMBIT; in fact, the GAMBIT code was forked from Cubit. As such, Carollo achieved an upgrade in their meshing capabilities while securing a gentle learning curve for their various users.
-
Streamlined usability: Coreform Cubit offers Carollo a comprehensive toolset for streamlining CAD preparation and mesh generation. Incorporating the 3D ACIS Modeler (ACIS) geometric modeling kernel, Coreform Cubit’s powerful simulation modeling capabilities allow users to build their simulation geometry of wastewater systems from scratch and then also create the mesh in the same software. Carollo also reports that the boundary layer technology in Coreform Cubit is superior to that of GAMBIT for their needs.
-
Diverse solutions: Coreform Cubit is an independent mesher and preprocessor that interfaces with over forty solvers, giving Carollo flexibility to explore different CFD solver solutions in the future.
-
Fair pricing: Coreform Cubit’s pricing is attractive and extremely competitive against other products available on the market.
Since Carollo’s transition in 2015, Coreform Cubit has served as a part of their daily workflow, increasing user confidence and saving valuable time and costs. See the figures below for an example of how Carollo uses Coreform Cubit to prepare accurate meshes to optimize flow and overall system efficiency in a wastewater treatment plant.
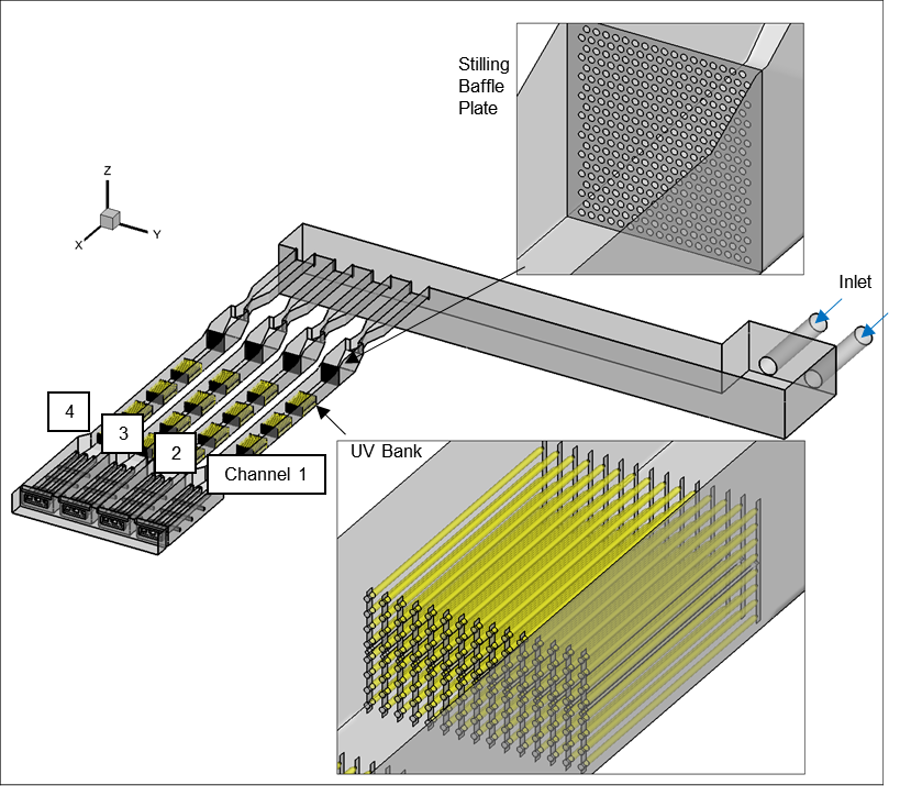
Figure 1: CFD model geometry developed by Carollo in Coreform Cubit for a wastewater treatment plant’s open channel ultraviolet (UV) disinfection system. Carollo often uses Coreform Cubit’s geometry creation tools to model simulation geometry directly in Coreform Cubit prior to meshing, rather than importing CAD data.
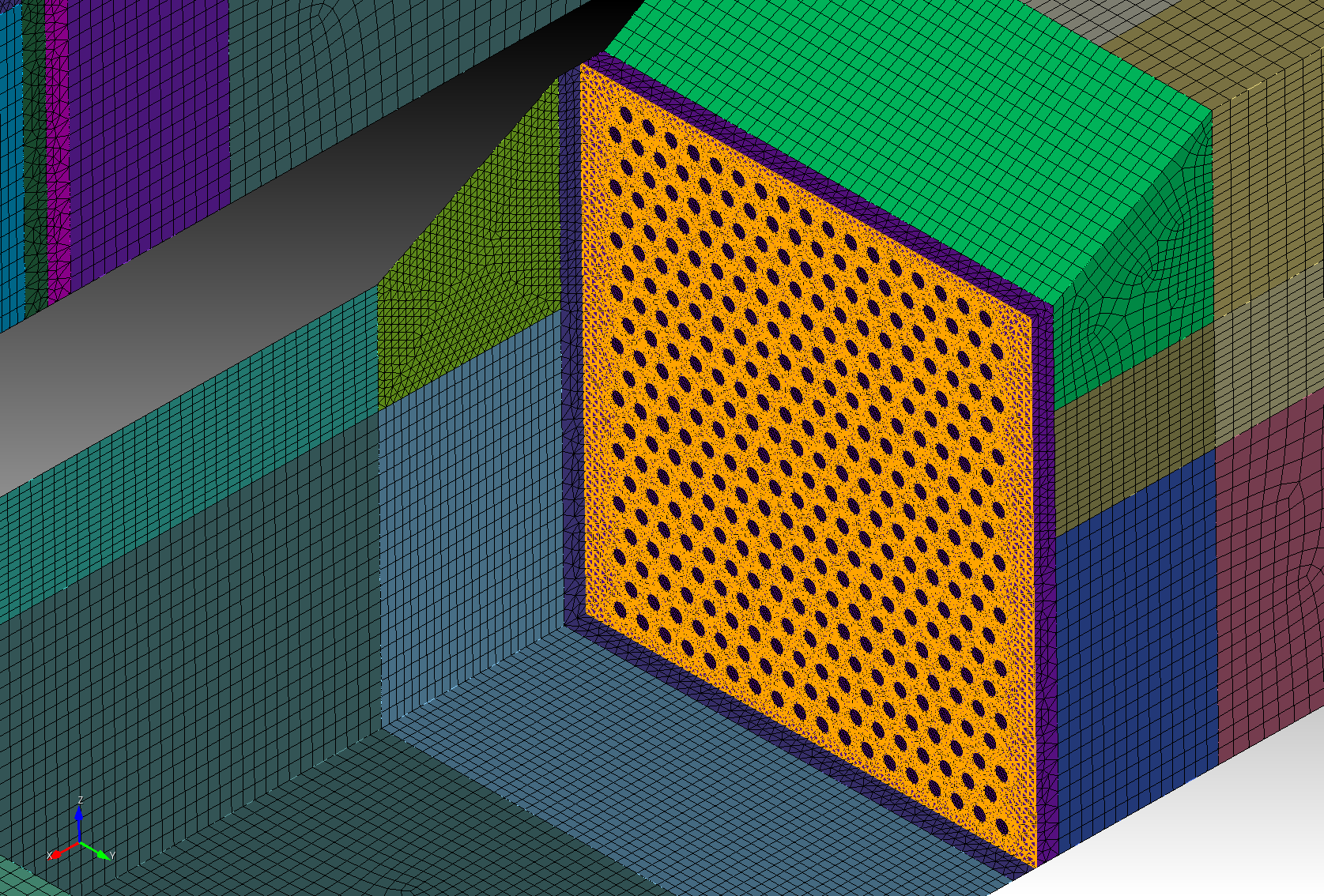
Figure 2: Mesh at an inlet stilling baffle plate generated using Coreform Cubit. For this mesh, Carollo used automatic tet meshing for the baffle plate to quickly and accurately capture the geometry, while using semi-automatic hex meshing to represent the surrounding channels for efficiency. The baffle plate consists of many small (~1-inch holes) that need to be accurately captured within a larger channel to adequately calculate the system hydraulics.
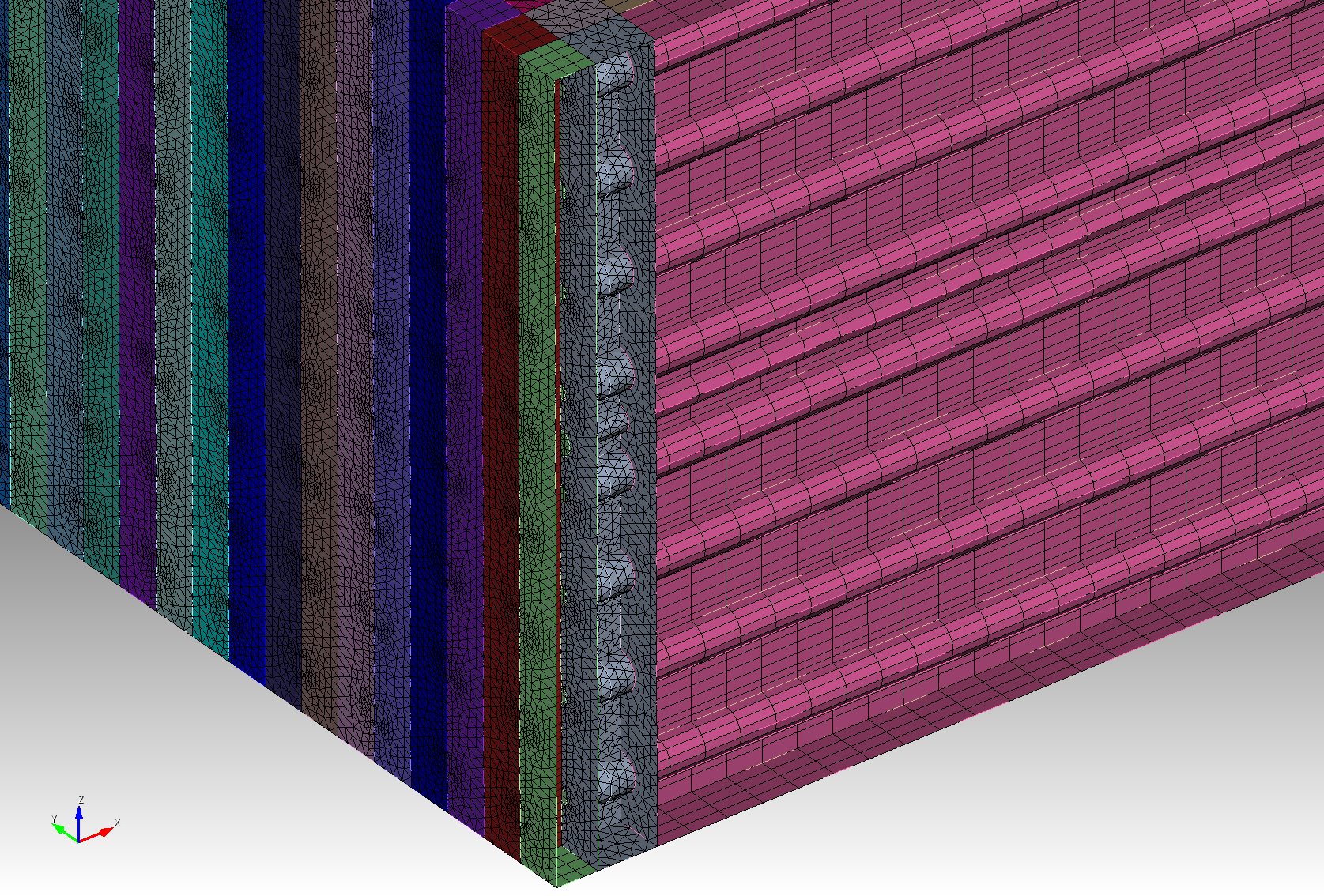
Figure 3: Mesh at UV banks created using Coreform Cubit. Capturing the bulk of the system details with hexahedral and prism elements leads to a high quality mesh, while minimizing the overall size for a computationally efficient solution.
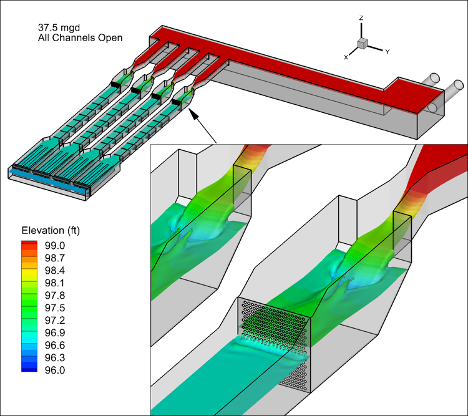
Figure 4: Overview of water surface elevations in a UV channel system. The simulation was run in ANSYS Fluent, with the mesh created in Coreform Cubit. The model is able to capture the free surface rapidly varied flow conditions through the Parshall flume and baffle plate, which both contribute to the hydraulics through the UV banks.
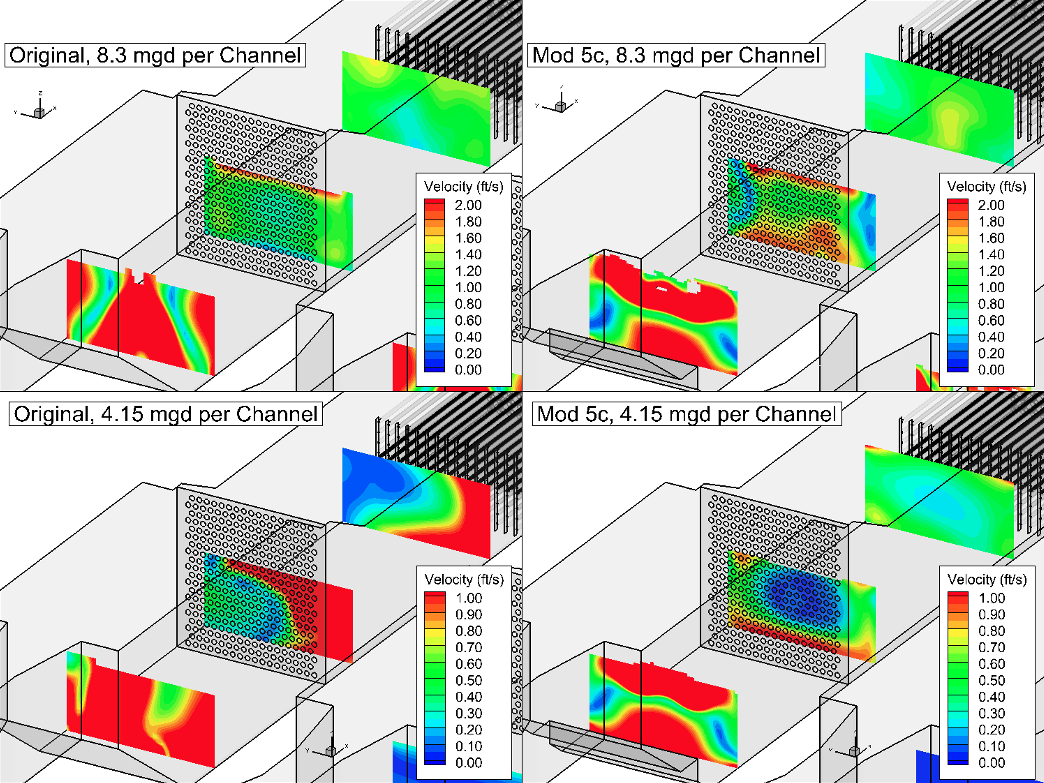
Figure 5: Comparison of velocity contours of the original design vs. modifications that improve the uniformity of the velocity approaching to the UV banks. A more uniform velocity field into the UV bank leads to more equal UV dose delivery to pathogens in the water flow, improving the overall system efficiency.