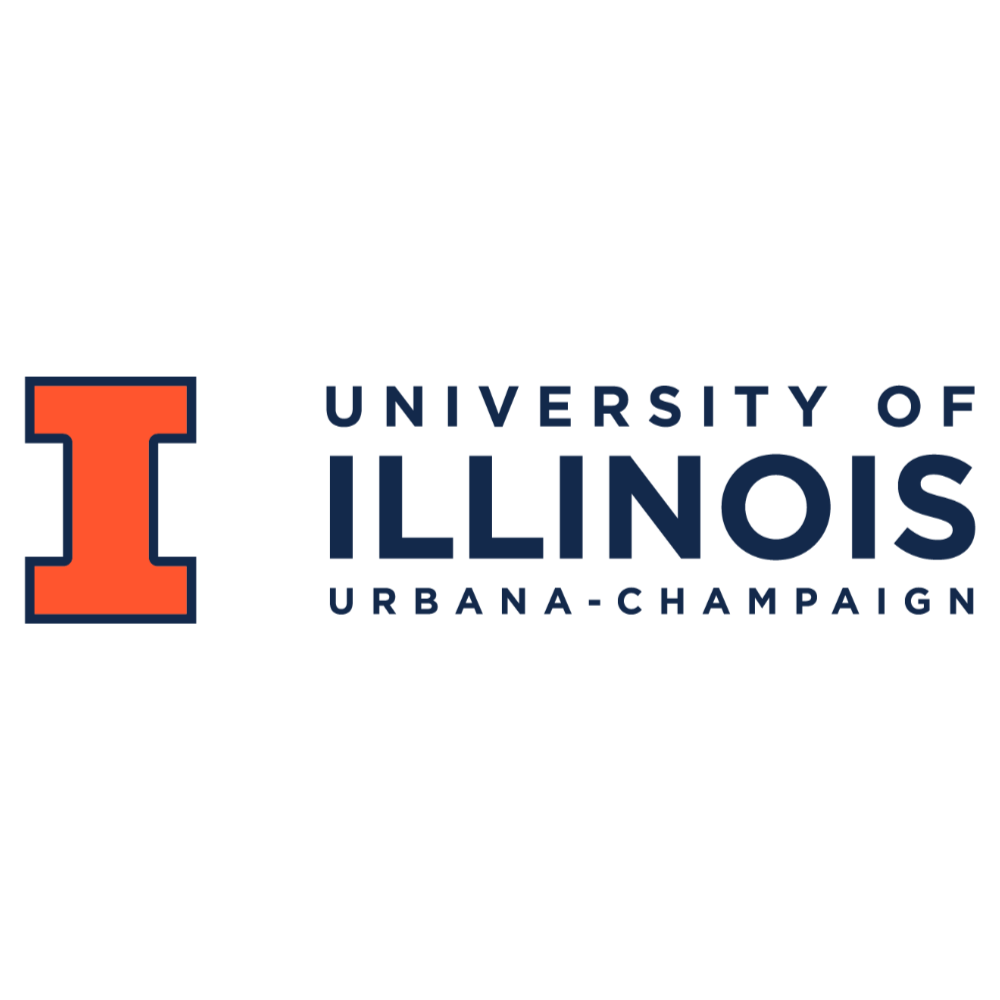
“Cardinal couples OpenMC to MOOSE using CAD geometry prepared in Coreform Cubit to enable integrated multiphysics simulations for nuclear systems.”
Dr. April Novak
Assistant Professor
University of Illinois Urbana-Champaign
Background
In nuclear engineering, multiphysics analysis is vital for understanding complex interactions between radiation transport and other physics phenomena, such as heat transfer, radiation transport, and material stresses. Traditional tools and workflows in nuclear multiphysics are often limited by complex software dependencies, incompatible data representations, and a steep learning curve, particularly when integrating constructive solid geometry (CSG) and computer-aided design (CAD) models.
Dr. April Novak, Assistant Professor at the University of Illinois Urbana-Champaign and lead developer of Cardinal, along with Dr. Patrick Shriwise, Computational Scientist at Argonne National Laboratory, sought to address these limitations by creating an accessible workflow using Coreform Cubit, OpenMC, MOOSE, and Cardinal. The goals are to streamline the nuclear multiphysics workflow, making it accessible to engineers and scientists across the field while preserving data accuracy and supporting high-fidelity, three-dimensional simulations.
Problem
The conventional approach to multiphysics simulations in nuclear engineering requires detailed knowledge of complex software stack integrations, creating a barrier for broader application. Key challenges include:
- Incompatible Data Models:Multiphysics workflows often start from CSG-based geometry representations, familiar in Monte Carlo simulations, but multiphysics workflows typically rely on CAD models for complex simulations like heat transfer or fluid dynamics.
- Loss of Data Fidelity in Conversions:Transitioning between CSG and CAD often results in data representation challenges due to the lack of meshes in CSG, which compromise precision or require labor-intensive adjustments.
- Manual Mesh Generation:Generating separate surface and volume meshes while preserving exact boundary alignment is necessary for criticality simulations but can be cumbersome, especially when scaling simulations to large, real-world models. Maintaining accurate and efficient data transfer between components adds complexity.
Dr. Novak’s team selected a representative model of the KRUSTY reactor—a compact nuclear reactor for space exploration applications—to develop and test an improved workflow. The KRUSTY reactor, comprising intricate geometrical structures and components, served as an ideal test case due to its important interactions between neutron transport and thermal heat transfer.
Solution
- Converting CSG to CAD for a Single Source of Truth By using the OpenMC CAD adapter, the team imported an existing OpenMC CSG model of the KRUSTY reactor fuel region directly into Coreform Cubit. This tool created an accessible CAD model of the reactor’s fuel region without the need to rebuild the geometry from scratch in CAD, saving significant time and reducing potential errors in geometry replication. The fuel region, once converted to CAD, became the central component of their workflow.
- Generating Conformal Surface and Volume Meshes Using Coreform Cubit’s integrated DAGMC functionality, the team created two meshes: a triangulated surface mesh for DAGMC to handle neutron transport, and a volumetric mesh for MOOSE’s heat conduction solver. Both meshes shared a common boundary, ensuring exact conformity and mass conservation across physics domains. This precise boundary alignment was critical for accurate data transfer, as it allowed for seamless power and temperature data exchange between the two components without interpolation errors or boundary inconsistencies.
- Implementing Temperature Feedback in Cardinal Cardinal facilitated real-time data transfer between OpenMC and MOOSE, using OpenMC to calculate the power distribution and MOOSE to compute the resulting temperature field. In this workflow, OpenMC’s power tally acted as a heat source for the MOOSE heat conduction solver. Cardinal then passed the temperature data back to OpenMC, which used it to update neutron cross-sections through Doppler broadening, a vital process for realistic simulations of nuclear reactors. Notably, Cardinal enabled the team to dynamically contour the CAD mesh based on temperature feedback, adapting the cell boundaries within the model as temperature distributions evolved. This contouring provided an adaptive meshing capability, allowing the simulation to achieve higher fidelity without requiring a predefined, finely meshed model. For the KRUSTY model, this feature enabled the simulation to represent realistic temperature distributions and their impact on neutron transport within the reactor’s fuel.
- Ensuring Energy Conservation By preserving exact boundary alignment and automating power and temperature data normalization between OpenMC and MOOSE, the workflow ensured that energy conservation was maintained at every step. Cardinal provided normalization and validation checks to verify power conservation, preventing data loss or errors in complex, iterative simulations.
- Visualizing 3D Results in Paraview Once the multiphysics simulations were complete, Dr. Novak’s team visualized results in Paraview, enabling them to inspect 3D temperature fields, power distributions, and neutron flux across the KRUSTY reactor fuel region. The 3D representation of these physics allowed the team to observe the effects of heat pipes on fuel temperature and the power profile, a critical insight for optimizing reactor performance in real-world applications.
Conclusion
Dr. Novak’s work demonstrates a significant advancement in the nuclear multiphysics workflow by combining traditional CSG-based neutronics with CAD-based multiphysics simulations, opening up opportunities for more accessible, accurate, and adaptable nuclear simulations. The KRUSTY reactor simulation marks a key step in enabling high-fidelity nuclear multiphysics analysis that is both accessible to new users and adaptable for complex reactor designs.
This new workflow promises to streamline simulations in industry applications, from initial design phases to benchmarking and validation for criticality safety and operational performance analysis. The results offer an accessible path for engineers and scientists to conduct high-fidelity multiphysics simulations without the constraints of traditional, complex data setups.