The leading developer of commercial spline-based simulation software, announces its receipt of a substantial government grant to explore a new method for simulating parts for 3D printed manufacturing.
Lattice structure patterns are becoming attractive to auto and airplane engineers because of their high strength-to-weight ratios. However, until now, these structures have been too complex for computers to be able to analyze them for things like stress reactions or collapse responses.
“Until now,” says Coreform CEO Matthew Sederberg, “without the ability to test parts via computer simulation, 3D printing of lattice structure in manufacturing has been largely relegated to prototypes and non-critical parts.”
The Coreform solution
Utah-based Coreform has developed an innovative technology that might solve this problem. Their patented flexible isogeometric analysis (Flex IGA) approach to simulation can handle the complexities of lattice structures with a much lower computational burden. In recognition of this technology’s potential, Coreform LLC has won a highly competitive government grant that will allow them to begin developing next-generation software for simulation of the lattice structures used in 3D printing. This grant, offered through the Federal Small Business Innovation Research (SBIR) program, is designed to support small businesses in pursuing innovative solutions to technological problems.
“We’re proud of Flex IGA, and proud that the SBIR program agrees that this is a valuable project to pursue,” says Coreform Director of Product Management Gregory Vernon. “We think this is absolutely going to change the game for deployment of 3D printed parts.”
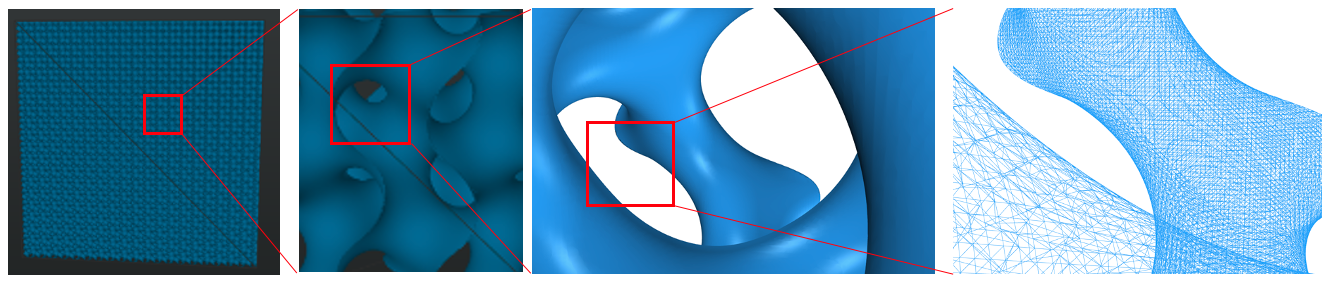
The difficulty of simulating lattic structures
3D printing allows manufacturers to print parts such as car bumpers with complex lattice microstructures that save material and weight. However, that low-weight approach makes the printed part vastly more complex to validate through simulation, because now the lattice microstructure has to be “meshed” into thousands of tiny elements itself (see the image above). The work of dividing those lattice structures into tiny parts for computation is too difficult and time-consuming to be practicable for any but small and simple parts. This is why 3D printing of lattice structures has not yet become widely-used.
Coreform’s Flex IGA process may make it possible to subdivide, or “mesh”, these complex microstructures with a minimum of time and expense. They anticipate using the SBIR grant to computer simulate a 3D-printed lattice structure that is more than ten times larger than any lattice structure that can be simulated today. If successful, Coreform’s technology will be key to making 3D printing a reality for manufacturers.
Keep up to date on Coreform’s progress
You can follow our progress by joining our forum. We have an active webinar series that features an upcoming event, “Introduction to Coreform IGA” that will demystify the isogeometric analysis (IGA) foundations of our technology. We will announce further developments in 3D-printing analysis here on our website and on our forum and on social media.
Try Coreform Cubit
he pre-processor of choice of engineers worldwide. Try Coreform Cubit free for 30 days.